How do I prepare floors and other surfaces for painting with a specialist industrial coating?
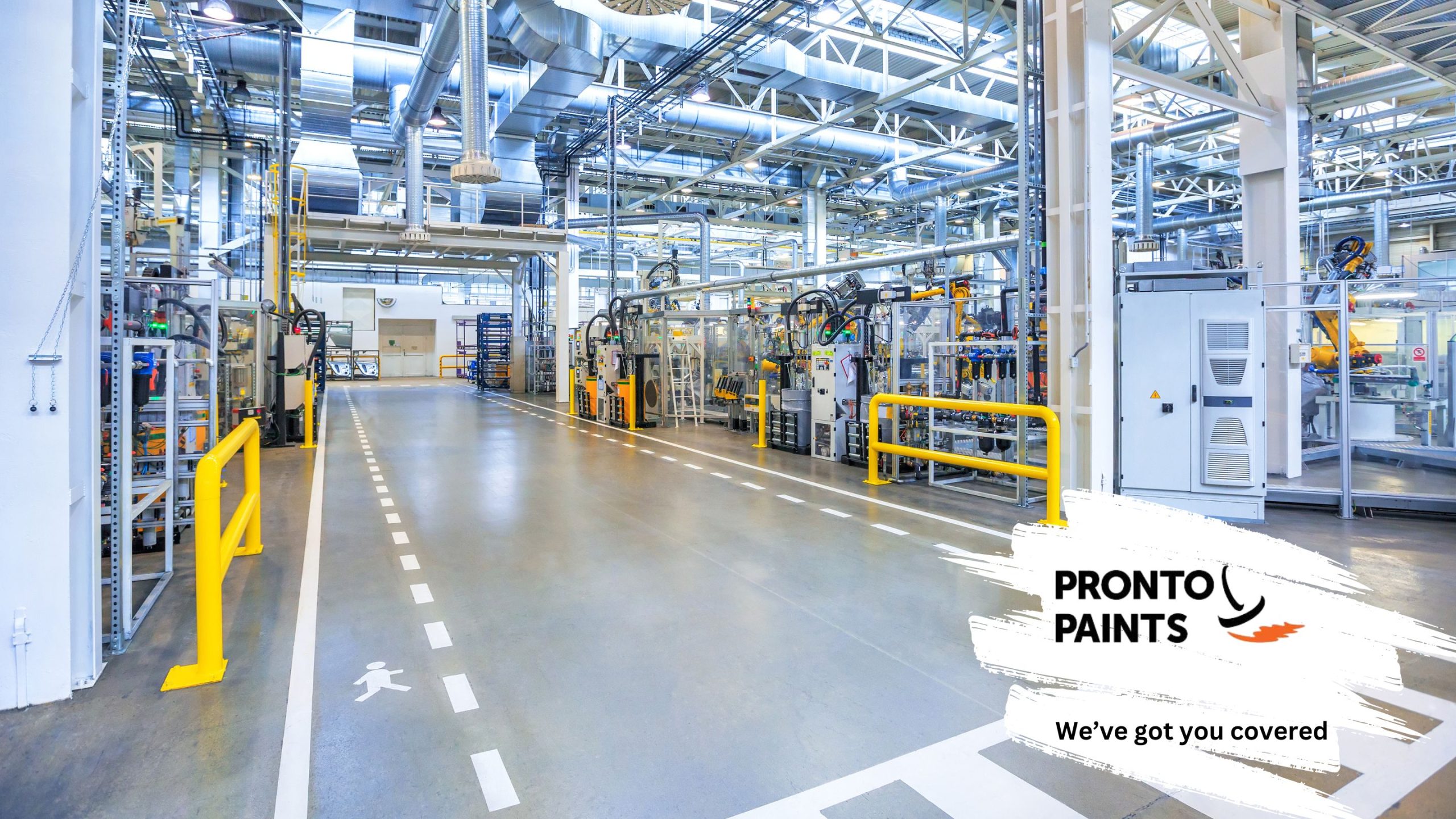
Proper surface preparation is essential to ensure that specialist industrial coatings adhere correctly, perform optimally, and provide long-lasting protection. Whether you’re preparing floors, walls, or other surfaces in an industrial facility, following a systematic preparation process is key to achieving a successful coating application.
Here’s how to prepare your surfaces effectively:
- Initial cleaning and degreasing
- Importance: Before any surface preparation begins, it’s critical to clean and degrease the surface thoroughly. Dirt, grease, and other contaminants can interfere with the adhesion of the coating and lead to poor performance over time.
- Process:
- Surface cleaning: Start by removing any obvious surface contamination using a steam cleaner or pressure washer, particularly in areas with heavy buildup of dirt or residues. Ensure the surface is completely dry before proceeding.
- Degreasing: Apply a suitable degreasing material liberally to the surface and allow it to absorb for a few minutes. This step helps to break down and loosen contaminants that may not be visible to the naked eye.
- Removal: Wipe the surface clean using lint-free absorbent paper towels or clean cloths. Avoid letting the degreasing solvent evaporate on its own, as this can leave contaminants behind. Repeat this process if necessary to ensure the surface is as clean as possible.
- Surface abrasion and roughening
- Importance: A key aspect of surface preparation is roughening the surface to create a ‘key’ that the coating can grip onto. This step is crucial for ensuring the longevity and durability of the coating.
- Process:
- Abrasive techniques: Depending on the material, use sandpaper, abrasive pads, or mechanical tools such as orbital sanders to abrade the surface. For metal surfaces, ensure all rust is thoroughly removed.
- Blast cleaning: For metal surfaces, blast cleaning is often the most effective method. It serves to both remove surface contaminants like rust or mill scale and to create a surface profile that enhances the adhesion of the coating.
- Surface profile: After blasting, ensure the surface profile (the roughness of the surface) is within the desired range, typically 25-50 microns. This profile is essential for the coating to adhere properly.
- Dealing with primed surfaces
- Importance: If the surface is already primed, it’s essential to ensure the primer is of good quality and well-adhered to the substrate. A poorly prepared or low-quality primer can undermine the entire coating system.
- Process:
- Inspection: Inspect the primed surface carefully. If there’s any doubt about the adhesion or quality of the primer, consider removing it entirely before applying a new coating.
- Flatting: If the primer is deemed acceptable, lightly sand (flat) the surface with appropriate abrasive paper or discs to provide a good key for the subsequent coating layers.
- Final cleaning and inspection
- Importance: After all abrasive work is done, it’s crucial to perform a final cleaning to remove any dust, debris, or residue that could affect the coating application.
- Process:
- Residue removal: Clean the surface of any sanding or blasting residues. This may involve using a vacuum, air blow-off, or a light solvent wipe to ensure no particles remain that could interfere with coating adhesion.
- Final degreasing: Once more, apply a light degreasing material to the surface to remove any final traces of contaminants. This final step ensures that the surface is perfectly clean and ready for coating.
General tips for surface preparation:
- Cleanliness standards: Adhere to recognised cleanliness standards, such as the Swedish Standard S.I.S. 055900-1967, to ensure the surface meets industry-accepted levels of cleanliness. For example, SA2½ (nearly white metal) is a common standard for industrial coatings.
- Consistent quality: Maintain consistency in your surface preparation routine to ensure every area of the facility receives the same level of attention, thus preventing weak points in the coating system.
- Environmental considerations: Ensure that the environment in which you are preparing and coating surfaces is controlled for temperature and humidity, as these factors can significantly impact both the preparation process and the coating application.
Proper preparation is the foundation of a successful industrial coating application.
By following these steps, you ensure that your specialist coatings perform to their full potential, providing long-term protection and maintaining the functionality and appearance of your facilities.
__
Pronto Paints have been working in facilities maintenance for over 30 years and have an exhaustively researched range of dedicated coatings. Click here to check out our technical specifications.
Want to book a callback or arrange a coating trial with one of our in-house experts? Drop an email to info@prontopaints.com
Further reading
What are the benefits of using specialist industrial coatings for facilities maintenance?
What are the best types of paints for facilities maintenance?